“Expanding the number of sites certified through ISCC PLUS adds credibility to our advanced recycling program and elevates CPChem’s contributions toward a circular economy for plastics.”
— Georgia Salisbury, Sustainability Circularity Lead
Drive the Development of Circular Products
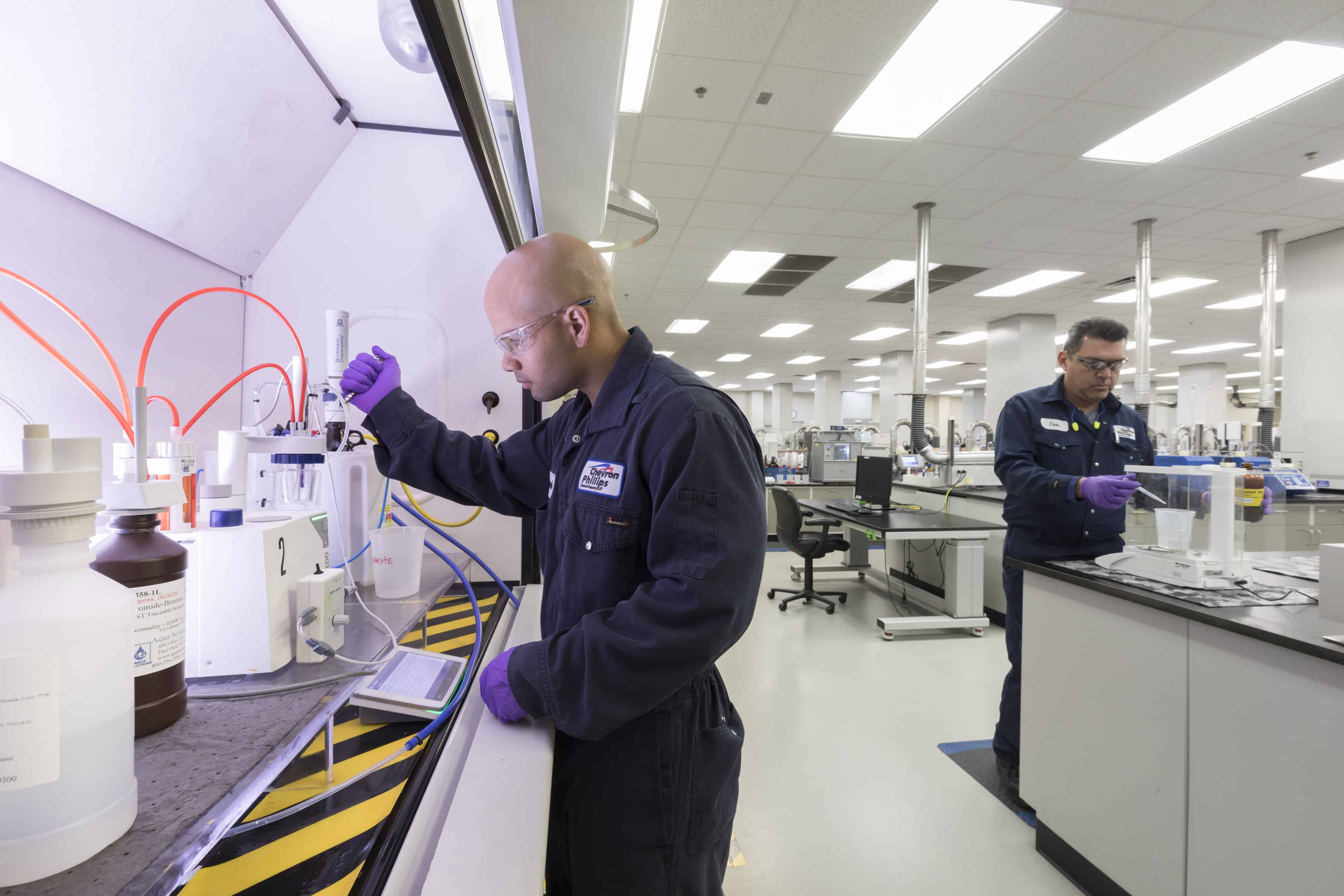
Reimagining the lifecycle of plastics is an essential part of reducing plastic pollution and supporting a more sustainable future. As a global leader in the production of olefins and polyolefins, CPChem is helping transform how we make, use and reuse plastics. With emerging recycling technologies and infrastructure, companies like CPChem can use advanced recycling to convert waste plastics into new polyethylene resins.
Developments in methods and technologies supporting increased circularity can give new life to plastics that were once considered difficult-to-recycle. Advanced recycling (also called chemical recycling) technologies convert hard-to-recycle plastics into raw materials that can be used to make new products. Because advanced recycled polymers have physical properties equivalent to their fossil-based counterparts, they may be selected for use in highly regulated applications not suitable for mechanically recycled polymers.
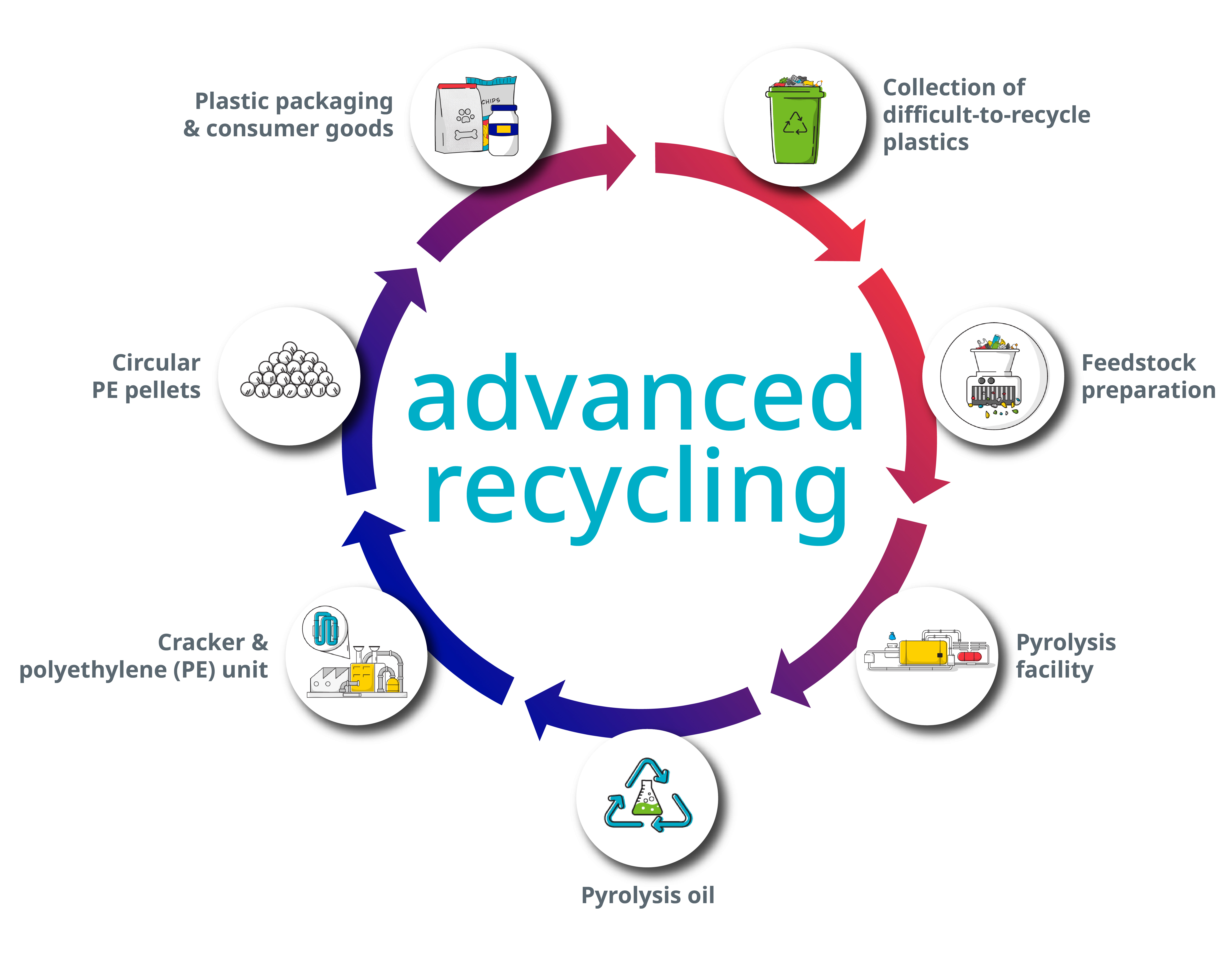
Click below to see how advanced recycling can breathe new life into plastic waste – again, and again, and again.
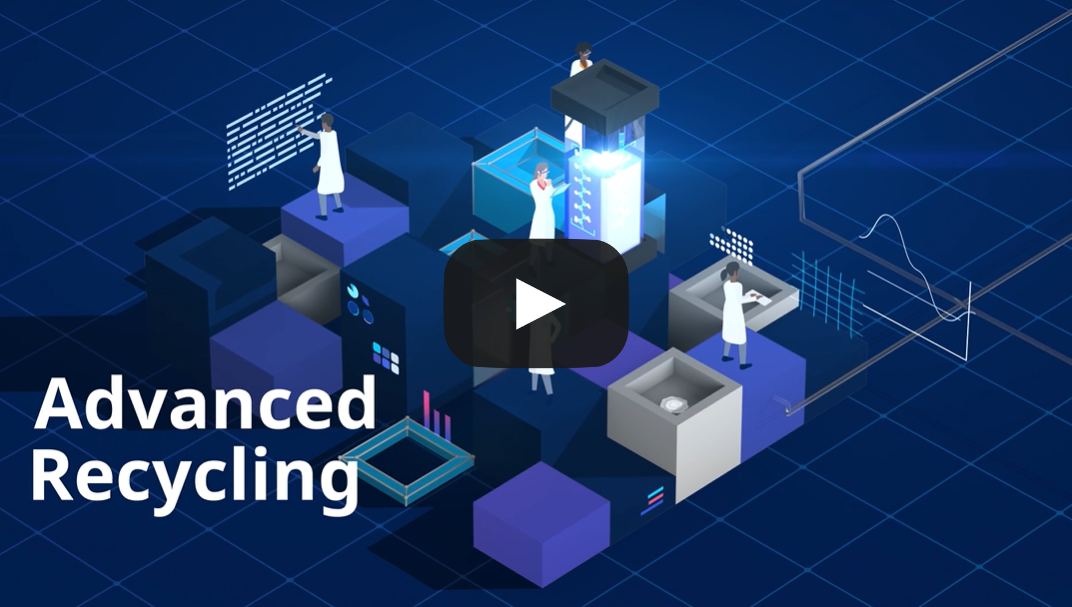
Advanced recycling processes are not meant to replace traditional mechanical recycling. Instead, conventional recycling methods and advanced recycling should be viewed as complementary and used in tandem to support efforts to keep plastics out of landfills.
Read about the difference between advanced and traditional recycling.
CPChem recognizes that collaboration across the value chain is essential to address plastic waste. We promote the development of circular products at our facilities worldwide through collaborations and investments in companies that convert plastic waste into virgin-grade feedstock to be used to create new, more sustainable products.
Marlex® Anew™ Circular Polyethylene
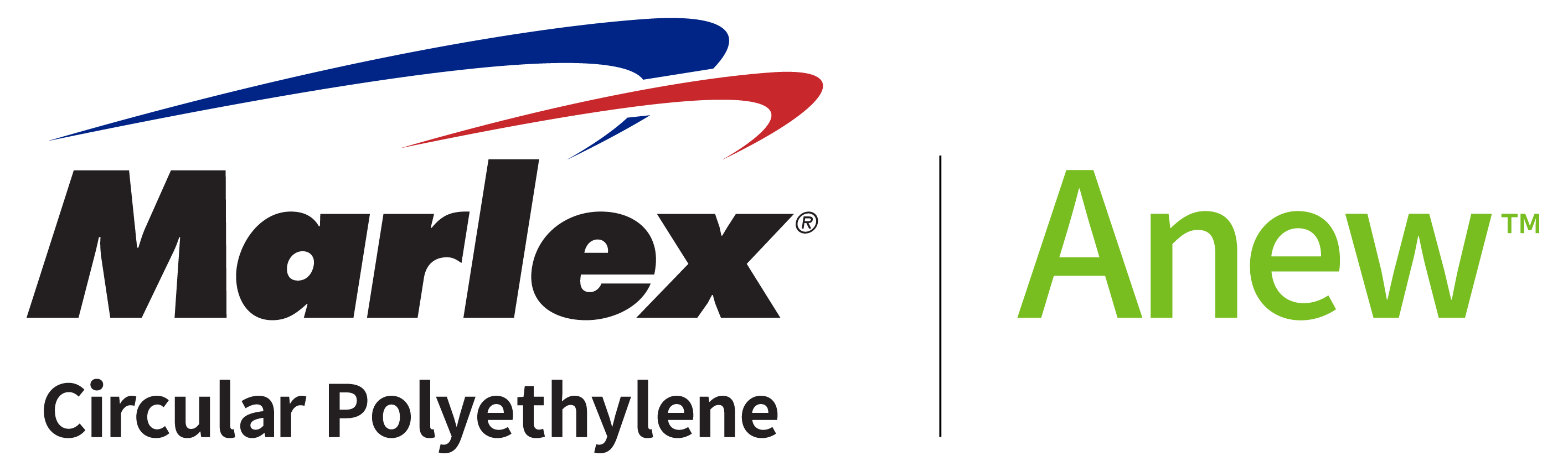
ISCC PLUS Certification
Marlex® Anew™ Circular Polyethylene is third-party certified by the International Sustainability and Carbon Certification PLUS system. Through rigorous annual audits, ISCC PLUS certification ensures Marlex® Anew™ Circular Polyethylene complies with the globally recognized sustainability and traceability requirements. To date, five CPChem manufacturing facilities are certified: Cedar Bayou, Orange, Pasadena and Sweeny/Old Ocean in Texas, U.S, and CPChem’s joint-venture facility in Singapore.
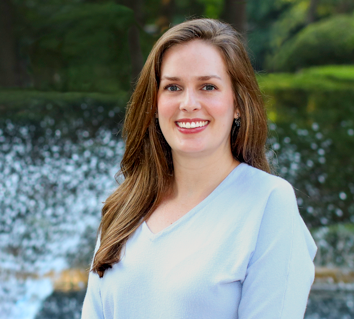
Leveraging advanced recycling and third-party certification to provide a circular product offering to our customers are just some of the ways we are working to achieve CPChem’s sustainability goals.
Download the Annual Sustainability ReportMeet Jacob: The Recycler

Senior Sustainability Engineer, Jacob Hilbrich, at CPChem’s Kingwood, TX, facility, is helping realize one of our sustainability targets: the large-scale production of polyethylene plastic using new, advanced technologies.
Read how CPChem’s Jacob Hilbrich is helping to change the pace of advanced recycling